1. 품질이 좋지 않습니다
재료, 공구 설계, 열처리, 가공 정확도, 페인트 품질 등은 표준에 맞지 않으므로 쉽게 두드리는 파손을 초래할 수 있습니다. 예를 들어, 탭핑 할 때 이동 치수 차이가 너무 크고 전환 필렛이 설계되지 않았으며 응력이 집중되며 쉽게 파손되기 쉽습니다. 손잡이와 공구 사이의 조인트의 단면 전달은 용접 분화구에 너무 가깝기 때문에 용접 응력과 응용 분야에서 복잡한 겹치는 응력면 농도가 크게 높아지고 TAP의 손상이 발생합니다. 사용.
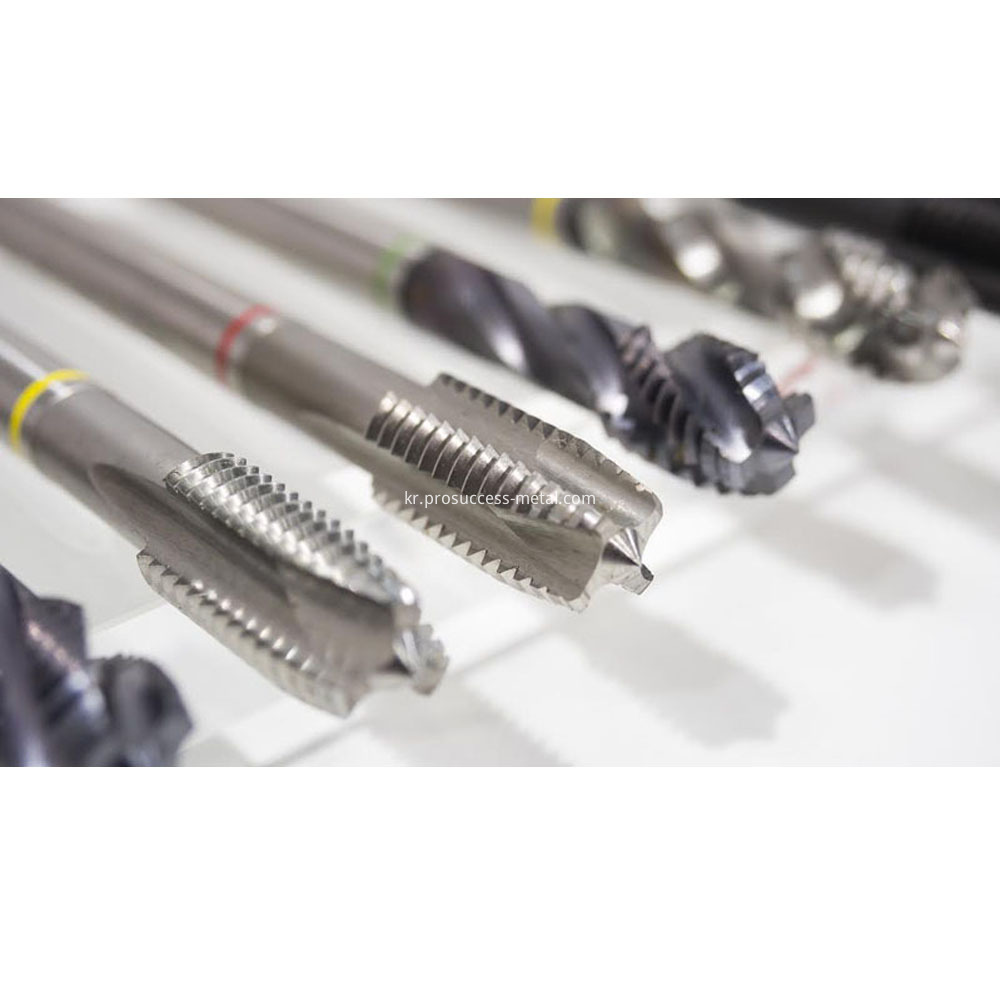
2. 불합리한 선택
경도가 높은 부품을 탭하려면 고속 스틸 탭, 탄화물 탭, 코팅 탭 등과 같은 고품질 탭을 선택해야합니다.
3. 태핑 도구는 재료 가공에 적합하지 않습니다
최근 몇 년 동안이 문제는 점점 더 많은 관심을 받았습니다. 과거에는 국내 제조업체가 항상 수입 테이핑 도구가 좋고 비싸다고 생각했습니다. 그러나 실제로 많은 국내 태핑 도구가 매우 적합합니다. 새로운 재료의 지속적인 증가와 처리의 어려움으로 인해 다양한 도구의 재료 도이 수요를 충족시키기 위해 증가하고 있습니다.
4. 하단 구멍의 구멍 직경이 너무 작습니다.
예를 들어, 0.5 mm 절단 플러그를 사용할 때, 철베이스 M5X를 가공하여 선택된 4.5 mm 직경 드릴 비트로 하단 구멍을 뚫습니다. 4.2mm 직경 드릴 구멍이 사용되면 태핑 공정에서 탭의 절단 부분이 증가하고 탭이 파손됩니다. 태핑 유형과 탭 부분의 재료에 따라 올바른 드릴 구멍 직경을 선택하는 것이 가장 좋습니다. 완전히 자격을 갖춘 드릴을 사용할 수없는 경우 더 큰 드릴을 선택할 수 있습니다.
5. 위치 문제
탭 부분은 더러운 재료로 만들어졌으며 제자리에 단단한 장소 또는 구멍이 있습니다. 그리고 즉시 끝은 균형과 파괴를 일으킨다.
6. 공작 기계는 정확도를 탭하는 요구 사항을 충족하지 않습니다.
기계 도구와 클램핑 몸체도 특히 고품질 수도꼭지에 매우 중요합니다. 특정 정밀도를 가진 공작 기계와 클램핑 바디만이 탭 역할을 할 수 있습니다. 불충분 한 동심성이 일반적입니다. 탭핑 시작시 태핑의 시작 및 위치가 잘못되었습니다. 즉, 메인 샤프트는 하단 구멍의 중심선과 동심이 아니지만 탭 사이의 토크가 너무 커서 주된 주된 이유입니다. 태핑의 파괴.
7. 절단 오일 및 윤활유의 품질 저하
많은 국내 기업들이 이것에주의를 기울이기 시작했습니다. 해외에서 절단 도구와 공작 기계를 구매하는 많은 회사는 매우 깊은 경험을 가지고 있습니다. 절단 오일 및 윤활유의 품질에는 문제가 있으며 가공 제품의 품질은 버 및 기타 부작용이 발생하기 쉽습니다. 동시에 서비스 수명이 크게 단축됩니다.
8. 불합리한 절단 속도 및 공급 속도
처리에 문제가있는 경우 대부분의 국내 사용자는 절단 속도와 공급 속도를 줄이기 때문에 탭의 구동력이 줄어들고 생성 된 스레드의 정밀도가 크게 줄어 듭니다. 결과적으로, 원사 표면의 거칠기가 증가하고 나사산 개구부 및 원사 정밀도는 제어 될 수 없습니다. 물론 볼츠와 같은 문제는 피할 수 없습니다. 그러나 너무 빨리 먹으면 수도꼭지 손상과 과도한 토크가 발생할 수 있습니다. 기계식 탭핑의 절단 속도는 일반적으로 강철의 경우 6 ~ 15m/분, 켄칭 및 강화 강철 및 단단한 강철의 경우 5 ~ 10m/분, 스테인레스 스틸의 경우 2 ~ 7m/분, 주철의 경우 8 ~ 10m/분입니다. 동일한 재료에서는 작은 탭 직경에 더 높은 값을 사용하고 더 큰 탭 직경의 경우 더 낮은 값을 사용하십시오.
9. 운영자의 기술과 기술은 요구 사항을 충족하지 않습니다.
위의 문제는 기술자의 운영자 판단 또는 피드백이 필요하지만 대부분의 국내 운영자는 현재 이러한 문제에 충분한주의를 기울이지 않습니다. 예를 들어, 블라인드 홀 스레드를 처리 할 때, 수도꼭지가 구멍의 바닥과 접촉 할 때, 조작자는 구멍의 바닥에 도달하기 전에 태핑 속도로 공급되지 않거나 칩 제거가 고르지 않을 때 공급해야합니다. , 탭이 파손됩니다. 운영자는 책임감을 높여야합니다.
위에서부터 공작 기계, 비품, 워크 피스, 프로세스, 척 및 도구 (예 : 도구)의 손상에 대한 많은 이유가 있음을 알 수 있습니다.